
Dr. Jordan Poler did not want to create an environmental problem by trying to solve one.
More than a decade ago, the University of North Carolina Charlotte professor decided to focus on chemistry that could be both sustainable and have minimum impact on the environment.
Supporter Spotlight
He believes he and his team of researchers have found that sweet spot, a secret sauce of nontoxic ingredients for a recipe that cleans per- and polyfluoroalkyl substances, or PFAS, and other toxins from drinking water at the point of use, think refrigerator filter for tap water.
Earlier this year, Poler was one of two UNCC professors awarded funding from NCInnovation’s grant program, which aims to help researchers at the state’s public universities get their products from lab to market.
And in an age when the idea of safe drinking water weighs heavy on North Carolinians whose water sources are contaminated by PFAS, what Poler said he has to offer could perhaps not come soon enough for consumers.
His research involves a process called ion exchange, which, in the most basic of explanations, works by trading an atom or group of atoms (ions) with ones that do not degrade the quality of drinking water.
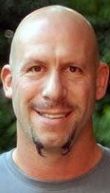
Ion exchange is by no means a novel concept. It was initially observed by two English chemists in 1850 and did not become widely used until the 1940s.
Supporter Spotlight
The chemistry developed in Poler’s lab is all water-based.
“There’s really no hazardous waste for our processing and the materials that we start with are all sustainable,” Poler said.
Those materials are a cocktail of sorts that include zeolite, an inexpensive and nontoxic, natural mineral that can be dug out of the ground, and cellulose, which comes from plants, trees and bushes.
“All of the agricultural waste and food waste can be turned into that other starting materials,” Poler said. “We’re really happy about that because we started off using materials that were kind of expensive and now we’ve developed this to basically reduce the cost of those types of starting materials to nearly zero relative to where we started with.”
The result are materials that can be packed into canisters made for water filtration in everything from refrigerators to well water systems.
These materials remove chemicals including pharmaceuticals, pesticides, arsenates, chromates, heavy metals such as iron, and, of course, PFAS.
The mix of materials remove very, very low concentrations of PFAS, down to the 4 parts per trillion maximum contaminant limits the U.S. Environmental Protection Agency established for six of the chemical compounds, including PFOA, PFOS, likely carcinogens, and GenX, a compound specific to the Chemours Fayetteville Works facility in Bladen County.
“It does a lot. It’s really quite a lovely hybrid, multi-use solution from a very green and sustainable approach,” Poler said.
PFAS are pervasive throughout North Carolina and the nation where they have been released into the environment by various manufacturing companies. PFAS are used in the production of a host of consumer goods, including food containers, stain- and water-resistant fabrics and firefighting foams.
Tests have detected these compounds in drinking water sources that are tapped by hundreds of public utilities throughout the state. PFAS have also been found in thousands of privately owned wells.
Exposure to PFAS has been linked to health effects including an increase in certain types of cancers, suppression of the immune system, low birth weight in infants and changes in liver function.
“It’s very hard to remove things at extremely low concentrations,” Poler said. “That’s why PFAS is such a challenge because it bioaccumulates. You can be drinking this water for years and then these problems creep in. So, ion exchange is, I think, the way to go.”
Poler founded a startup called naneXPure LLC, a company that is, by all accounts at the moment, a placeholder, but one intended to translate the technology developed in his lab into the marketplace.
He and his business partner are working with Monroe-based Goulston Technologies to broaden the drinking water purification materials crafted in his lab to industry scale.
The materials being developed in his lab are regenerable and reusable. That means that, unlike refrigerator filters that must be replaced every six months or so, what he has developed can be made good as new.
Regenerating materials not only cut down on plastic waste, but they keep used, discarded filters out of landfills and, therefore, out of leaching back into the environment.
Say you have a system that’s good for purifying 100,000 liters of water.
“It’s 100,000 liters of very low-contaminated water, but you don’t want to drink that contaminant so you’d purify it,” Poler said. “And then, when we regenerate it, we have maybe one liter of highly contaminated regenerate that can then be very easily destroyed by other types of technologies.”
The materials developed in Poler’s lab will have to be certified by the National Sanitation Foundation. Funding for that testing will be covered under the $400,000 NCInnovations grant Poler received.
Poler’s idea is that consumers would initially buy two cartridges. When materials in the first cartridge that is used needs to be replaced, that cartridge could be shipped back for regeneration in a mailer that would be provided by the company.
“It might be pie in the sky,” Poler said. “But that’s been my long-term goal.”
The technology has the potential to be used on a larger, water utility-type scale.